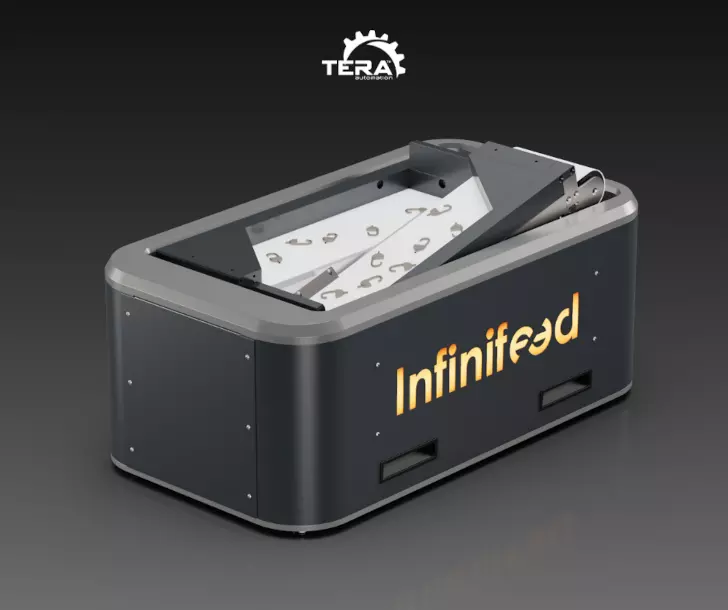
A key element in Industrial Robotic
Infinifeed™ is a power system - featuring integrated App - for products of different shapes weighing.
Compact, versatile, and user-friendly - it is a brand-new product embodying both Tera Automation’s expertise as integrators and Doma Automation’s as developers.
The role of power systems in Industrial Automation
In Industrial Automation, power systems are machines that make the handling of items for robots easier.
It is a simple activity that yet determines the good result of the entire process. Power systems must in fact be connected to a 2D vision system that detects the items and signals the robots about which one to pick up.
It is therefore essential that power systems guarantee a continuous and regular supply and that they can manage the widest range of shapes and dimensions.
Then: an integrated power system. Now: a stand-alone product. Thanks to a partnership project.
It all started with our T-Loop Feeder™ power system, which was specifically designed to work together with our robotic cell for CNC machine tending T-Flexicell™.
T-Loop Feeder™ allowed the robot to pick up one piece at a time in order to put it in the zero-adjustment template before the CNC machining phase. The system was solid and reliable but bound to the core features of the robotic cell.
Here at Tera, we wanted instead to transform that power system in a new, stand-alone product that could be integrated to any other machine, in any production field.
Our willing to renew our T-Loop Feeder™ led us to a close collaboration with Doma Automation, a company based in Arezzo that can already boast 15 years of experience in software for jewellery.
Putting our expertise together, we started designing the new Infinifeed™ power system.
First goal: user-friendliness.
When we first started the Infinifeed™ project, our main goal was to reach a level of quality that enabled us to be competitive on the market.
Regarding the hardware, there is not much difference from a product to another. So, the task is quite easy: positioning items homogenously on a surface for robot handling and continuous supply of the handling circuit.
When it comes to the software, on the other hand, it is all more complicated, because there are 3 elements involved in the process and they must communicate with each other: the robots, the vision system, and the supplier.
Programming the software for smooth communication among these 3 elements requires highly specialised skills that are not always available in companies.
These considerations led us define our new goal: Infinifeed™ would first of all be a user-friendly supplier that doesn’t need any highly specialised skills to be installed and managed.
From the idea to success, it was a short walk. Infinifeed™ is now manageable from its integrated App that features not only remote control but also configuration and integration with the robot and vision system.
It will be enough to take a picture with the mobile phone of the object to be picked up by the robot, type the exact gripping point on the photo and send the information to the vision system.
In addition, it will be possible:
- change the speed of the belts
- control general operation (startup and shutdown) in real time
- be constantly updated on any operating alerts.
A totally renewed hardware system
Compared to its predecessor T-Loop Feeder™, Infinifeed™ also has several improvements on the hardware side:
- fluidity of the circuit and reduction of interlocking.
With Infinifeed™ we have eliminated any physical elements that could interfere with the recirculation of the parts. The two belts on which the parts circulate are adhered to each other and the passage of the parts from one belt to the other takes place by gravity without banks or conveyors. This choice has also reduced the cases of interlocking between the pieces themselves. - integrated electronic parts.
The product has been simplified as much as possible and the app is the only user interface. - simplified disassembly.
The shell and sides are magnetically removable, which makes maintenance (e.g. for replacing the electronic board) and cleaning easy (the conveyor belts can be removed for cleaning). - reclining belts.
Depending on the size and weight of the workpieces, the inclination of the belts can be modified. - optional illuminator.
When gripping with a vision system, Infinifeed™ can be equipped with an illuminator (bottom up). This makes the pieces stand out. - optional tilting pistons.
Electric pistons, with light belt percussion, allow the parts to be distributed and tilted to the best gripping side. - no use of compressed air.
All drives are electronic.
In conclusion, the new feeding system developed by Tera in cooperation with Doma Automation ensures maximum efficiency for companies thanks to its intuitive software and state-of-the-art hardware.
Thanks to Infinifeed™
- specialised skills will no longer be required
- setup times will be drastically reduced
- companies will be constantly connected to their Infinifeed™.