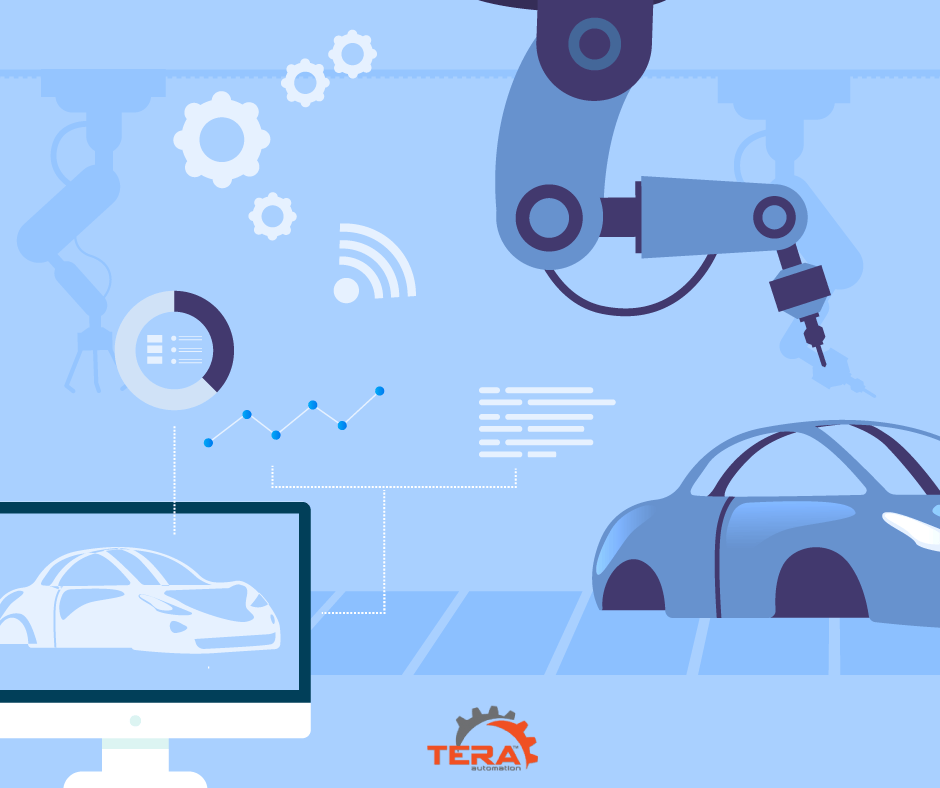
Cos’è il Digital Twin?
Il digital twin può essere definito l’equivalente virtuale di un prodotto, di un processo o di un servizio, ma anche di infrastrutture, dispositivi o sistemi. È un clone, un alter egovirtuale, che trova la massima applicazione nel settore dell’Internet of Things, in cui quasi la metà delle aziende impiega questa tecnologia.
Il gemello digitale è lo stato dell’arte dell’Industria 4.0. Questo significa che le smart factories possono contare su un modello virtuale in grado di implementare la produzione, ottimizzare le risorse e risolvere criticità e anomalie.
Come funziona un gemello digitale?
Il digital twin è una rappresentazione digitale dell’originale, di cui contiene tutte le informazioni a livello meccanico, geometrico ed elettronico. Tra il prodotto e il suo clone virtuale ci devono essere dei sistemi di collegamento per garantire un flusso continuo di dati e informazioni.
Sostituendo un modello virtuale alla realtà, le aziende possono lavorare direttamente sulla copia. In questo modo non c’è bisogno di creare prototipi fisici per la progettazione né di intervenire sul prodotto reale per la manutenzione.
Si evita, soprattutto, di arrivare a situazioni di blocco per anomalie o manutenzioni riparative, poiché lo studio del digital twin e la lettura dei dati trasmessi in tempo reale consentono di svolgere attività di manutenzione preventiva.
Il digital twin rappresenta un vantaggio competitivo per le aziende, che possono utilizzare la tecnologia del modello virtuale per abbattere tempi e costidi manutenzione, ridurre i rischi e sviluppare nuove opportunità di business.
Opportunità strategiche
Il digital twin rappresenta un’incredibile opportunità di crescita per l’Industria 4.0 perché permette di ridurre inefficienze e costi di manutenzione. Consente sia l’analisi dei dati in tempo reale che il monitoraggio dei sistemi. In questo modo le aziende riescono a prevenire i problemi, perché simulando il comportamento possono prevedere e quindi evitare guasti e irregolarità.
Oltre che per la produzione, svolge un ruolo fondamentale per l’ideazione e la progettazione. Le aziende riducono tempi e costi di sviluppo e hanno l’opportunità di mettere a punto nuovi prodotti utilizzando la simulazione invece dei modelli reali, molto più dispendiosi in termini di costi, tempo e risorse umane.
Guidare l’innovazione, quindi, ma anche migliorare i prodotti già esistenti, rendendoli sempre più performanti. Il digital twin, in questo caso, permette alle aziende di seguire tutto il ciclo di vita di un prodotto, o di un sistema, così da rilevare in modo immediato eventuali problematiche e anomalie.
Avere uno strumento di correzione significa alzare il livello dei nostri servizi, stabilire nuovi standard qualitativie occupare una posizione assolutamente privilegiata all’interno del mercato.
In sintesi, possiamo dire che il gemello digitale opera su due fronti, quello sperimentale e quello predittivo L’attività sperimentale è la molla propulsiva per l’ideazione e lo sviluppo di nuovi prodotti. Piuttosto che creare un costoso prototipo fisico ci si affida allo studio del digital twin per trovare e risolvere eventuali criticità senza dover mettere in campo modelli reali.
Per quanto riguarda l’attività predittiva, invece, abbiamo visto come l’impiego del digital twin permetta di prevedere in anticipo anomalie, rischi ed errori di sistema. L’analisi dei dati e il monitoraggio dei sistemi fanno sì che i problemi vengano risolti ancora prima che si verifichino.
Una volta individuate le criticità, soprattutto, è possibile intervenire in modo assolutamente mirato per modificare il prodotto originale reale e raggiungere la massima funzionalità.
Il digital twin segue prodotti, servizi o sistemi complessi in moltissimi settori, per tutto il loro ciclo di vita. Dalla progettazione allo sviluppo, dalla produzione ai sistemi di vendita, dalla manutenzione all’assistenza non c’è una sola fase per cui il gemello digitale non rappresenti un vantaggio insostituibile.
Industria 4.0 e Digital Twin
Abbiamo già analizzato il rapporto tra automazione industriale e controllo dei processi di lavoro. Come abbiamo visto, l’analisi dei dati è fondamentale al successo di un’azienda.
Oltre al monitoraggio in tempo reale, il digital twin consente una condivisione delle informazioni raccolte all’interno di tutta l’azienda. La standardizzazione dei processi, inoltre, permette di raggiungere gli obiettivi aziendali a livello globale, poiché tutte le fabbriche sparse nel mondo vengono gestite in maniera semplice e immediata proprio grazie ai cloni virtuali, accessibili in qualunque momento e da qualunque luogo.
Il vantaggio competitivo è ancora più rilevante per tutte le aziende che forniscono supply chain collaborative come terze parti. Oltre a fornire prodotti o componenti altamente performanti, queste factories possono garantire la massima trasparenza informativa dalla progettazione alla produzione. Per l’azienda che deve scegliere a quale supply chain affidarsi, il digital twin diventa una leva impareggiabile.
Il digital twin, quindi, è una replica virtuale che permette di raccogliere dati e monitorare il sistema in tempo reale con lo scopo di:
- prevedere e prevenire anomalie, rischi o criticità
- migliorare le prestazioni dei prodotti e dei sistemi esistenti
- svolgere manutenzione preventiva prima di arrivare al guasto o all’inattività forzata
- testare e capire come si comporteranno i sistemi e i prodotti che si vogliono realizzare
L’Industria 4.0, attraverso l’automazione industriale, mira alla creazione di nuovi modelli di business e all’aumento della produttività e della qualità. Il digital twin diventa l’alleato perfetto per il successo, perché riesce a eliminare i tempi di inattività non pianificati e i costi di manutenzione, migliorando produttività ed efficienza.